Сьогодні у світі існує три види плоского скла: метод плоского малювання, метод флоат-скла та каландрування. Флоат-скло, на яке зараз припадає понад 90% від загального обсягу виробництва скла, є основним будівельним матеріалом у світовому архітектурному склі. Процес виробництва флоат-скла був заснований у 1952 році, що встановило світовий стандарт високоякісного виробництва скла. Процес виробництва флоат-скла включає п'ять основних етапів:
● інгредієнти
● плавлення
● формування та покриття
● відпал
● різання та пакування
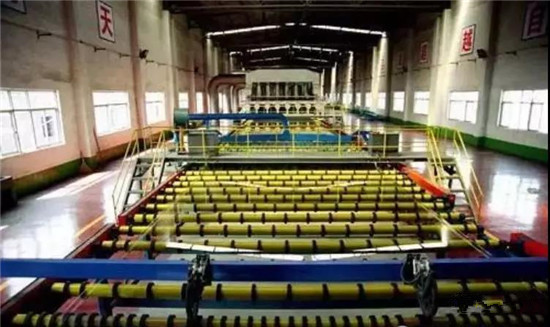
Інгредієнти
Дозування – це перший етап, на якому готують сировину до плавлення. Сировина включає пісок, доломіт, вапняк, кальциновану соду та мірабіліт, які транспортуються вантажівками або поїздами. Ця сировина зберігається в кімнаті для дозування. У матеріальному приміщенні є силоси, бункери, конвеєрні стрічки, жолоби, пилозбірники та необхідні системи керування, які контролюють транспортування сировини та змішування шихтових матеріалів. З моменту доставки сировини до матеріального приміщення вона постійно переміщується.
Усередині дозувального відділення довга плоска конвеєрна стрічка безперервно транспортує сировину з дозувального відділення шар за шаром до ковшового елеватора, а потім відправляє її на ваговий пристрій для перевірки їхньої загальної ваги. До цих інгредієнтів додаються фрагменти переробленого скла або повернуті з виробничої лінії матеріали. Кожна партія містить приблизно 10-30% битого скла. Сухі матеріали додаються в змішувач і змішуються з шихтою. Змішана шихта надсилається з дозувального відділення до силосу верхньої частини печі для зберігання через конвеєрну стрічку, а потім додається в піч з контрольованою швидкістю за допомогою живильника.

Типовий склад скла
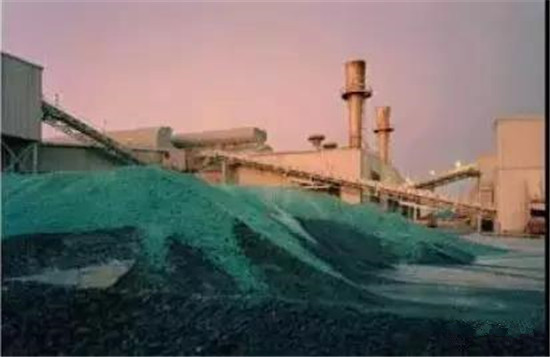
Склобійний двір
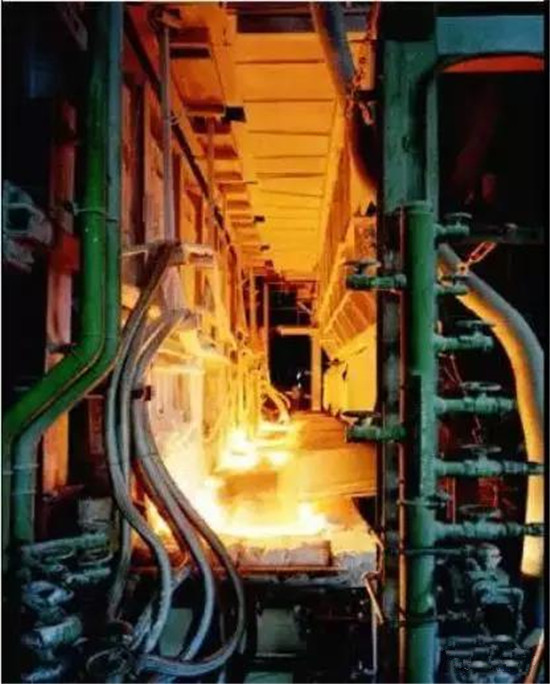
Подайте змішану сировину у вхід печі до 1650 градусів за допомогою бункера
Плавлення
Типова піч – це піч з поперечним полум'ям та шістьма регенераторами, шириною близько 25 метрів та шириною 62 метри, з добовою виробничою потужністю 500 тонн. Основними частинами печі є плавильний басейн/освітлювач, робочий басейн, регенератор та мала піч. Як показано на рисунку 4, вона виготовлена зі спеціальних вогнетривких матеріалів та має сталеву конструкцію на зовнішній рамі. Шихта подається до плавильного басейну печі за допомогою живильника, а плавильний басейн нагрівається до 1650 ℃ за допомогою газового розпилювача.
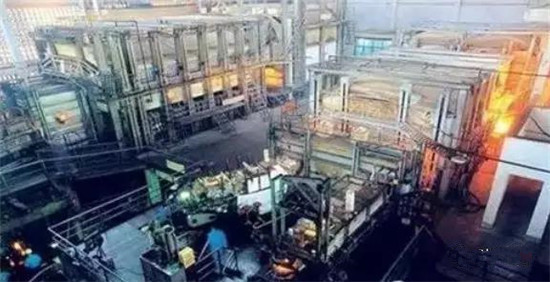
Розплавлене скло перетікає з плавильної ванни до області горловини через освітлювач і рівномірно перемішується. Потім воно потрапляє в робочу частину та повільно охолоджується приблизно до 1100 градусів, щоб досягти потрібної в'язкості перед потраплянням у ванну з оловом.
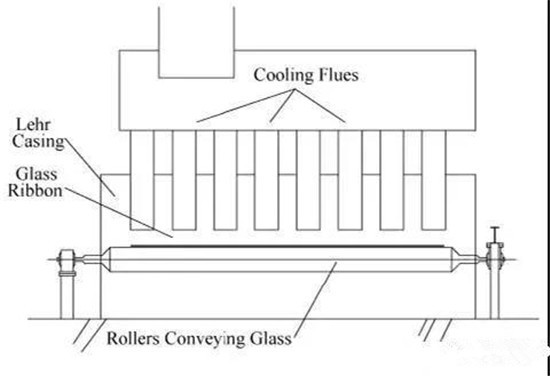
Формування та покриття
Процес формування освітленого рідкого скла у скляну пластину – це процес механічної маніпуляції відповідно до природної тенденції матеріалу, а природна товщина цього матеріалу становить 6,88 мм. Рідке скло витікає з печі через канал, і його потік контролюється регульованими дверцятами, які називаються плунжером, що знаходиться приблизно на ± 0,15 мм у рідке скло. Воно плаває на розплавленому олові – звідси й назва флоат-скло. Скло та олово не реагують одне з одним і можуть бути розділені; їхній взаємний опір у молекулярній формі робить скло більш гладким.
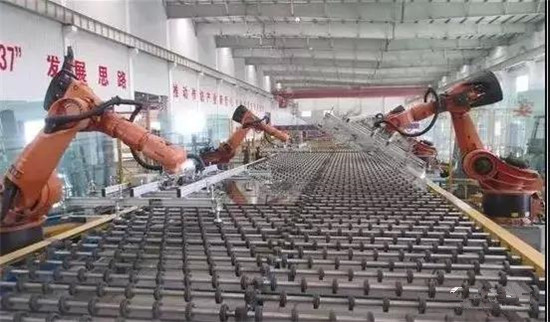
Ванна являє собою блок, герметично заповнений контрольованою атмосферою азоту та водню. Вона включає опорну сталь, верхню та нижню оболонки, вогнетриви, олово та нагрівальні елементи, відновлювальну атмосферу, датчики температури, комп'ютерну систему керування процесом, має ширину близько 8 метрів та довжину 60 метрів, а швидкість виробничої лінії може досягати 25 метрів за хвилину. Ванна з оловом містить майже 200 тонн чистого олова із середньою температурою 800 ℃. Коли скло утворює тонкий шар на кінці входу ванни з оловом, його називають скляною пластиною, і з обох боків працює ряд регульованих краєзнімачів. Оператор використовує програму керування для встановлення швидкості печі для відпалу та краєвитягувальної машини. Товщина скляної пластини може становити від 0,55 до 25 мм. Верхній перегородковий нагрівальний елемент використовується для контролю температури скла. Оскільки скляна пластина безперервно протікає через ванну з оловом, температура скляної пластини поступово знижується, роблячи скло плоским та паралельним. На цьому етапі можна використовувати acuracoat® для нанесення покриття на поточну лінію на світловідбиваючу плівку, низькоемісійну плівку, сонцезахисну плівку, фотоелектричну плівку та самоочисну плівку на піролізному CVD-обладнанні. На цьому етапі скло готове до охолодження.
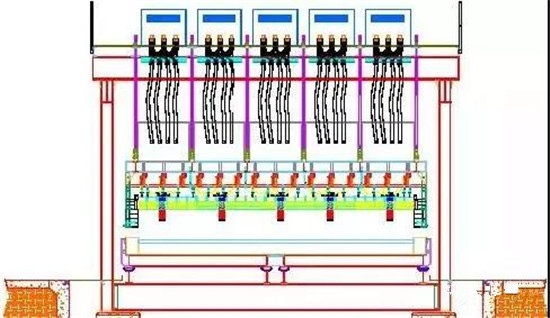
Поперечний розріз ванни
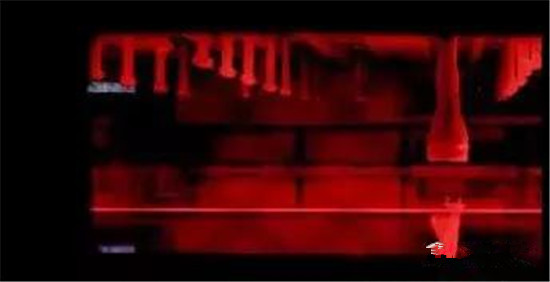
Скло розподіляють тонким шаром по розплавленому олову, тримають окремо від олова та формують у тарілку.
Підвісний нагрівальний елемент забезпечує подачу тепла, а ширина та товщина скла контролюються швидкістю та кутом краєзнімного механізму.
Відпал
Коли сформоване скло залишає олов'яну ванну, температура скла становить 600 ℃. Якщо скляну пластину охолоджувати в атмосфері, поверхня скла охолоджуватиметься швидше, ніж внутрішня частина скла, що призведе до серйозного стиснення поверхні та шкідливого внутрішнього напруження скляної пластини.
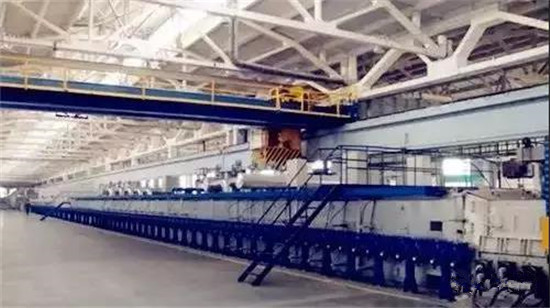
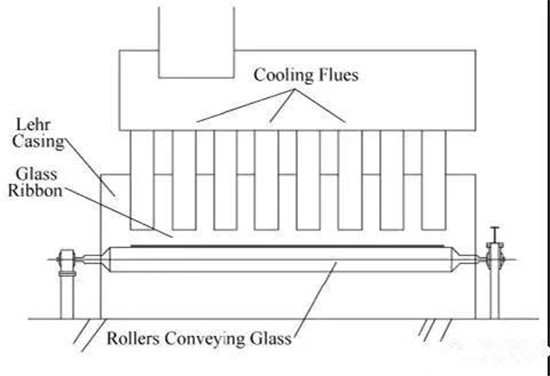
Розділ печі для відпалу
Процес нагрівання скла до та після формування також є процесом утворення внутрішніх напружень. Тому необхідно контролювати нагрівання, щоб поступово знижувати температуру скла до температури навколишнього середовища, тобто проводити відпал. Фактично, відпал проводиться в печі для відпалу з попередньо встановленим градієнтом температури (див. Рисунок 7) шириною близько 6 метрів та довжиною 120 метрів. Піч для відпалу включає електрично керовані нагрівальні елементи та вентилятори для підтримки стабільного поперечного розподілу температури скляних пластин.
Результатом процесу відпалу є те, що скло ретельно охолоджується до кімнатної температури без тимчасового напруження або напруги.
Різання та упаковка
Скляні пластини, охолоджені в печі для відпалу, транспортуються до зони різання через роликовий стіл, з'єднаний з приводною системою печі для відпалу. Скло проходить онлайн-систему контролю для усунення будь-яких дефектів, а потім ріжеться алмазним різальним кругом для видалення краю скла (матеріал краю переробляється як склобитий матеріал). Потім його ріжуть на розмір, необхідний замовнику. Поверхня скла посипається порошковим середовищем, щоб скляні пластини можна було складати та зберігати, щоб уникнути злипання або подряпин. Потім бездоганні скляні пластини розділяються на стопки для пакування за допомогою ручних або автоматичних машин і перевозяться на склад для зберігання або відправлення клієнтам.
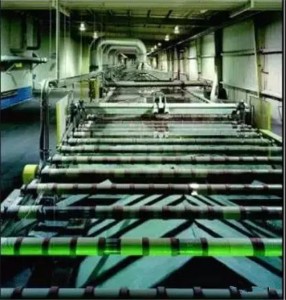
Після того, як скляна пластина залишає піч для відпалу, скляна пластина повністю формується та переміщується до зони охолодження для подальшого зниження температури.